One of the first lessons any disaster responder learns is that there is always another storm. Whatever the natural disaster currently being responded to in whatever community suffering through it, it will not be the last that community faces. Team Rubicon decided years ago that the best time to respond to disaster is before it strikes by giving local communities and individuals the materials and knowledge necessary to prepare themselves and their homes for the inevitable tornado, hurricane, or fire.
When Team Rubicon launched the Rebuild program, it was to help homeowners protect themselves against future storms, as well as recover from past ones. The goal isn’t simply to renovate a home—Greyshirts want families to have the peace of mind that their home can withstand the next wave of what’s coming.
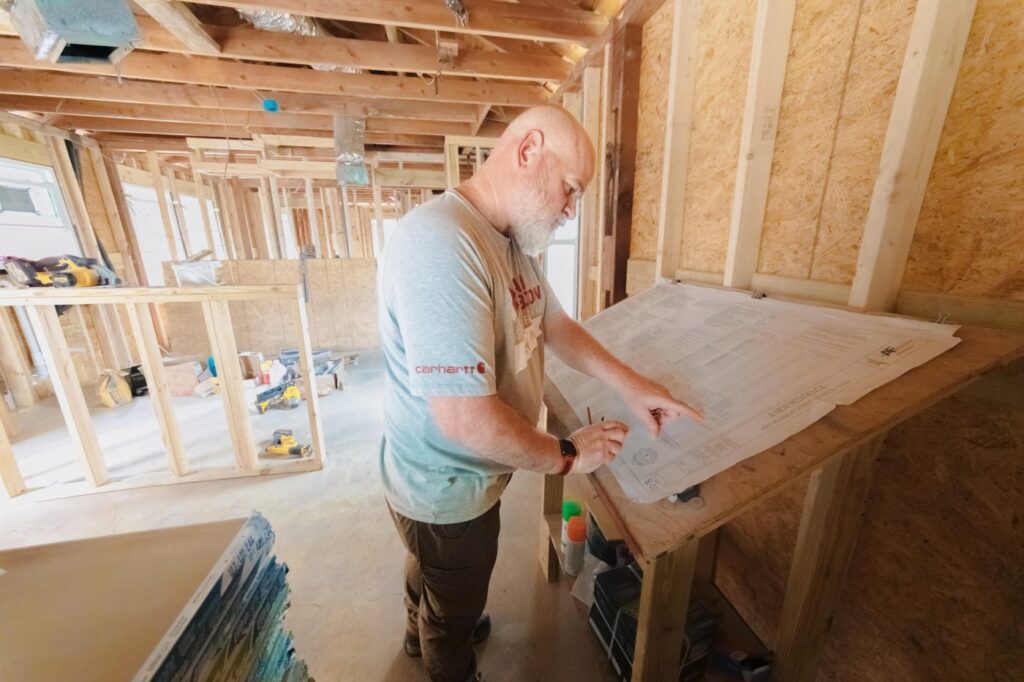
That’s why the organization is adopting the Fortified Home™ standard, as created by the Institute for Business and Home Safety (IBHS), for their rebuild projects whenever and wherever possible. By focusing on resilience and using resilient building materials and techniques whenever possible, homeowners are equipped with greater levels of disaster readiness. Today, Team Rubicon is the only organization to repair and retrofit a storm-damaged home and receive the FORTIFIED Gold certification on the home.
Fortified Gold is the highest designation issued by the voluntary construction and reconstruction program developed by IBHS. In addition to a more durable roof and impact protected windows, its requirements include a continuous load path. That means the roof is tied to the walls and the walls are anchored to the foundation. This level of protection is designed to toughen homes against all manner of severe weather, including hail, hurricanes, and even tornadoes.
“Fortified Gold means that your house is going to be able to act as a system and it can stand up in a severe storm,” says Fred Malik, managing director of Fortified at IBHS. “If you have to evacuate, it’s going to be there for you to return to.”
Designing to the Fortified standard goes beyond building codes; it is a nationally recognized construction method based upon decades of research, and Team Rubicon is one of few nonprofits that utilizes Fortified in rebuilding and retrofitting homes impacted by disasters. The techniques and materials used in Fortified homes are meant to stand up to some of the most severe weather Mother Nature can throw at them and are tested to do that in real-world conditions, as well as in a very big laboratory.
“We have a giant wind tunnel in South Carolina,” explains Malik, “like a very large airplane hangar with 105 fans generating up to 130 mph winds.” Within that wind tunnel, IBHS built two 2-story houses and simulated a powerful severe wind storm, to see just how much Fortified materials can protect. IBHS replicates everything from hailstorms to hurricane-force and to tornado-strength winds and rain in the wind tunnel, testing housing materials and building techniques against what they can be expected to encounter.
“In the last five years or so, over 90% of our 45,000 homes have been through at least one hurricane and we know that those houses performed better than their standard-built peers,” says Malik.
As IBHS works to create new, resilient products, and construction methods to help build new, more durable houses, Team Rubicon is integrating them into old, devastated homes. “It’s often difficult to be able to retrofit to the Fortified Gold and Fortified Silver conventions,” explains IBHS CEO Roy Wright. “What Team Rubicon has uniquely done is say, ‘It’s not too hard for us.’”
Many of the homes chosen for Team Rubicon’s Rebuild program have been, if not thoroughly gutted by nature, rendered so unlivable that the first thing to do is to gut the house by hand. Greyshirts will strip the home down to the frame, and then build it back up. And once there is a bare husk of a house, why not use the Fortified homes standard to rebuild it to a level that won’t be at risk again?
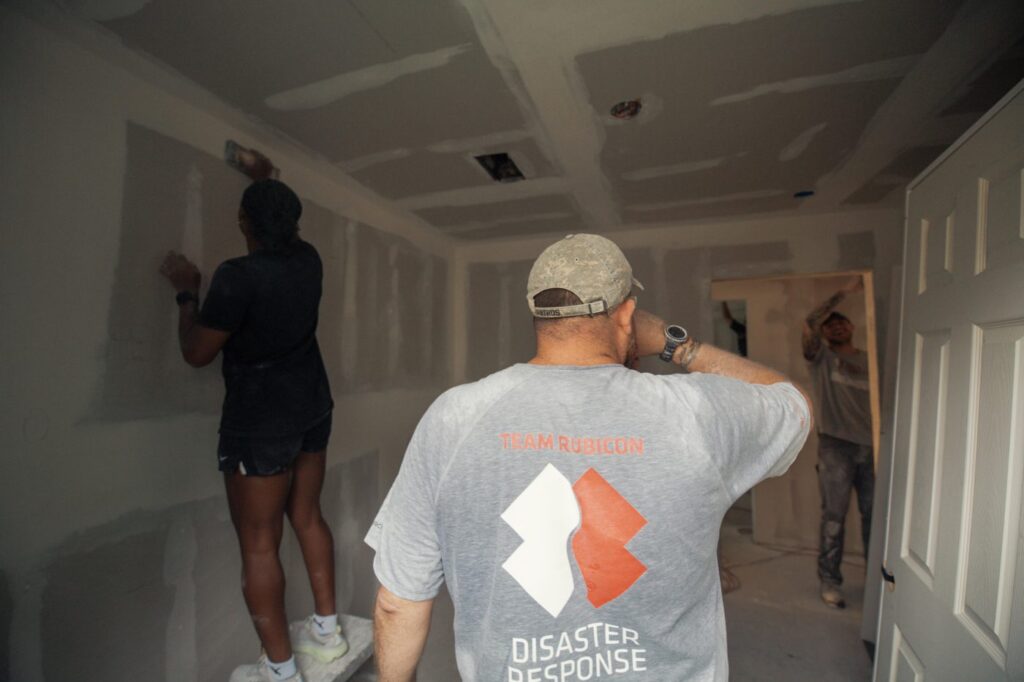
“The goal of IBHS is to reduce avoidable loss and avoidable disruption for homeowners,” says Malik, “Team Rubicon has taken the approach that if we’re taking the expense of stripping so much out of the home, down to the studs, it’s a perfect time to add Fortified material.”
“Insurance companies across the industry look at Team Rubicon and say, ‘this is a place where the science that IBHS developed gets put it into action in a way that addresses the real needs of people and communities.’ It’s the only way to do it,” says Wright.
Designing homes properly to withstand what Mother Nature can do means creating layers of protection. Take, for example, IBHS guidelines for resilient shingles and roofs. “We design for the day when the winds do blow them off, and underneath the shingles is a sealed roof deck,” explains Wright. “If you lose the roof cover, you don’t have water in the house. Team Rubicon has put those pieces in motion.”
“We want to work with folks we trust,” says Wright, “Team Rubicon, in its very DNA, is a veteran-driven organization that is committed to meeting people at their time of greatest need, those core values resonate with us at IBHS.”
What nature can do, of course, varies depending on location. Just as IBHS tests materials for all kinds of hazards, Team Rubicon has been rebuilding after all kinds of disasters, in all kinds of places. Since the Rebuild program began in 2017, Team Rubicon has rebuilt and repaired more than 200 homes everywhere from Haines, AK, to Selma, AL, with the largest rebuild operations happening in Texas and the Gulf Coast region. In some communities, Team Rubicon has built new construction from the ground, including in Puerto Rico where it built three new homes and rebuilt 500 roofs. Combined, the Fortified Gold standard and the IBHS team are helping Team Rubicon assist homeowners during their time of greatest need, whatever disaster created that need, in a secure way designed for their situation.
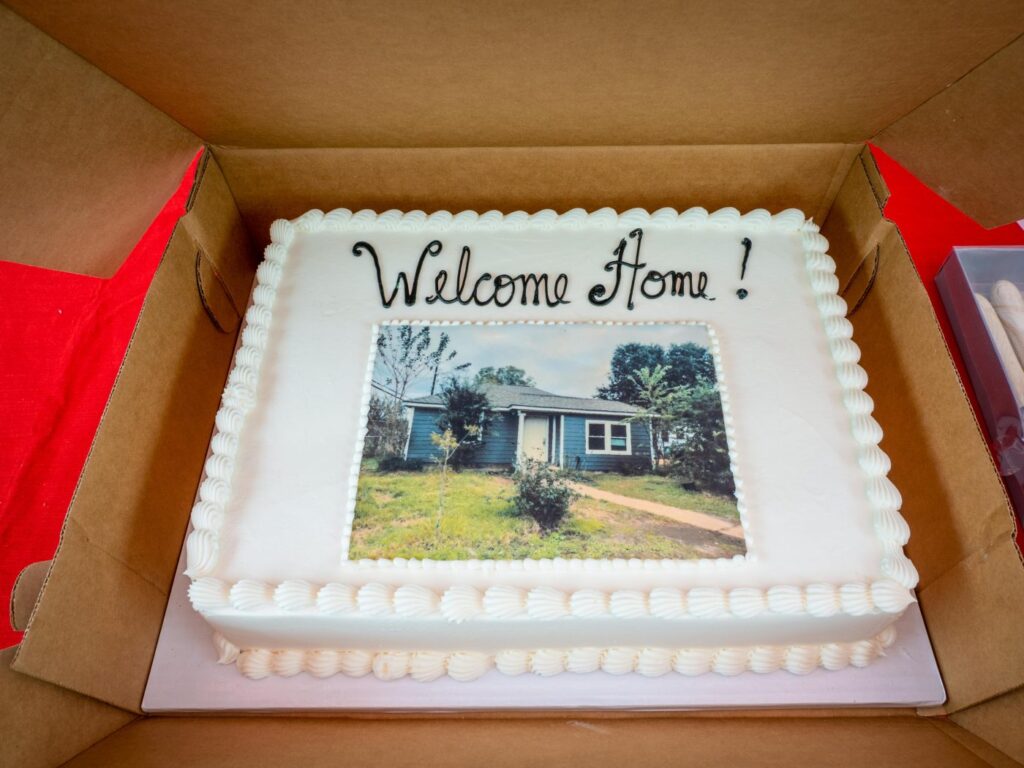